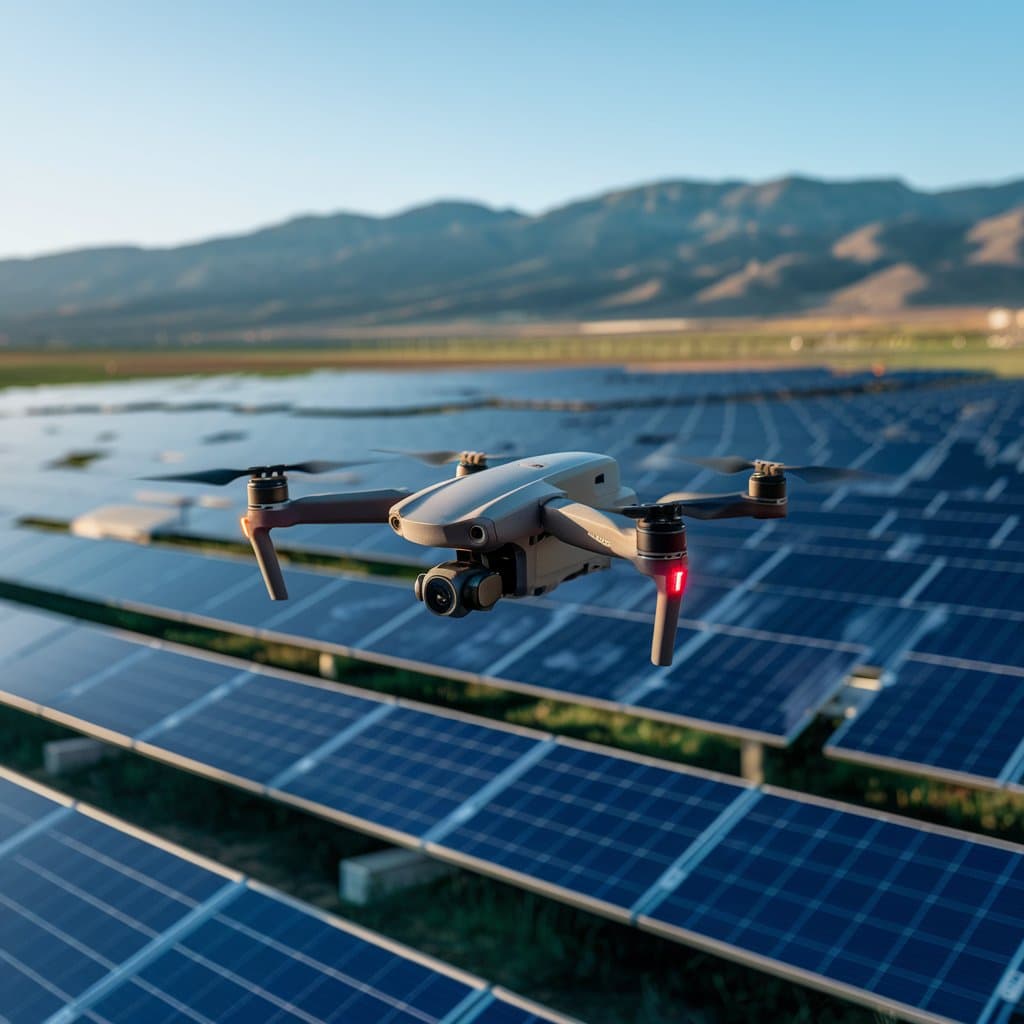
Renewable energy
Green Energy
Solar Panel Inspection & Monitoring
A few common defects observed during inspection of the solar farm as under :
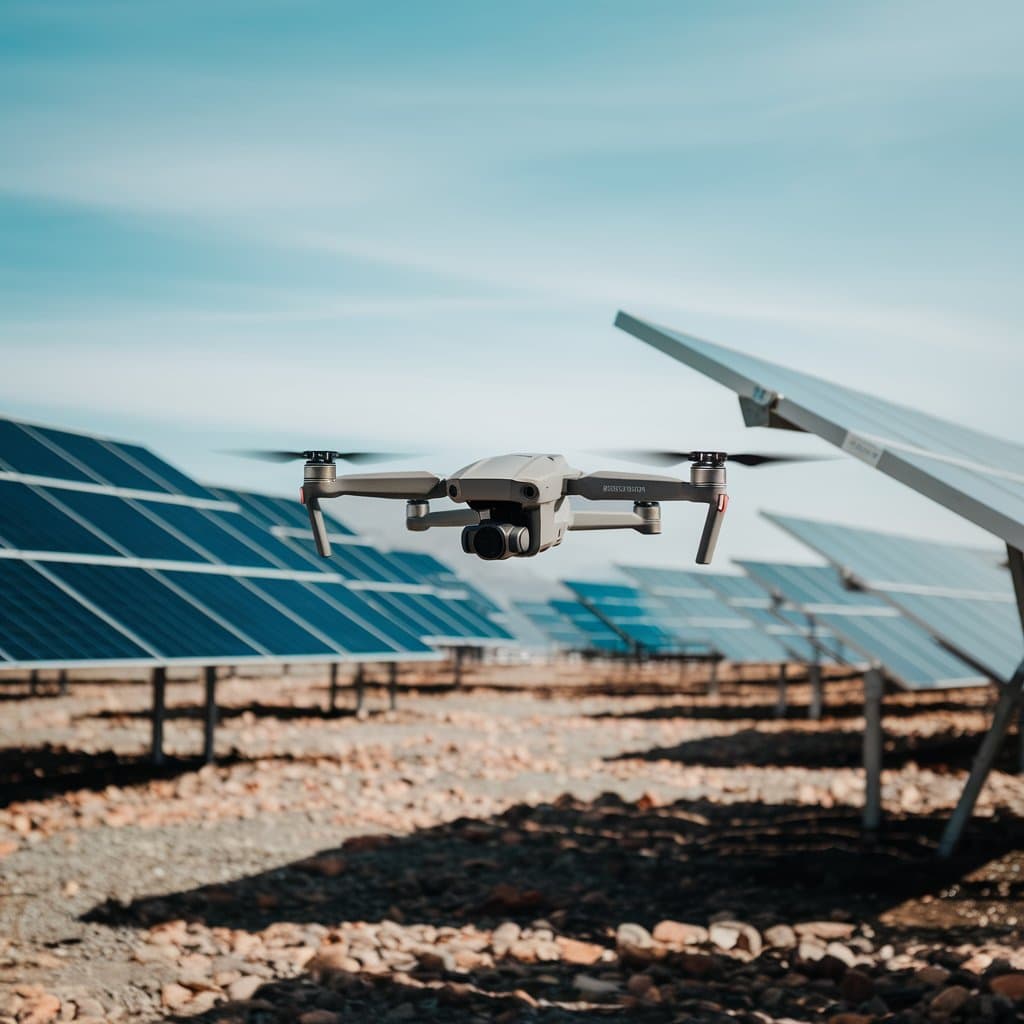
- Cell Mismatch Defect. Cell mismatches in photovoltaic (PV) cells can significantly impact system output and yield, potentially leading to hotspots causing browning, burns, or fire.
- Cracks . Defects in photovoltaic systems, resulting from manufacturing processes, handling, packaging, transport, and reloading, and harsh climates like strong winds, snow, and hail, are common throughout their lifetime.
- Discolorations . PV systems can suffer from discoloration due to internal components like low-quality polymers or external factors like high temperatures and humidity, reducing sunlight entry and causing significant losses.
- Delamination . Through a PV modules’ lifetime, adhesive bonds between solar cells’ materials can begin to hold moisture, causing severe delamination. These defects can also occur due to improper lamination methods and harsh weather conditions.
- Hotspots . Overloaded regions on solar panels can cause warm spots due to poorly soldered cell connections or structural flaws, resulting in increased resistance and short-circuits, depreciating the productivity and goodwill of the PV system.
Benifits you get
Cell Mismatch Defect
Cell mismatches in photovoltaic (PV) cells can significantly impact system output and yield,potentially leading to hotspots causing browning, burns, or fire.
Cracks
Defects in photovoltaic systems, resulting from manufacturing processes, handling, packaging, transport, and reloading, and harsh climates like strong winds, snow, and hail, are common throughout their lifetime.
Discolorations
PV systems can suffer from discoloration due to internal components like low-quality polymers or external factors like high temperatures and humidity, reducing sunlight entry and causing significant losses.
Delamination
Through a PV modules’ lifetime, adhesive bonds between solar cells’ materials can begin to hold moisture, causing severe delamination. These defects can also occur due to improper lamination methods and harsh weather conditions.
Hotspots
Overloaded regions on solar panels can cause warm spots due to poorly soldered cell connections or structural flaws, resulting in increased resistance and short-circuits, depreciating the productivity and goodwill of the PV system.
Our Deliverables in the Asset Inspection
Cracks
Common defects caused by handling, packaging, transport, and harsh climates over time.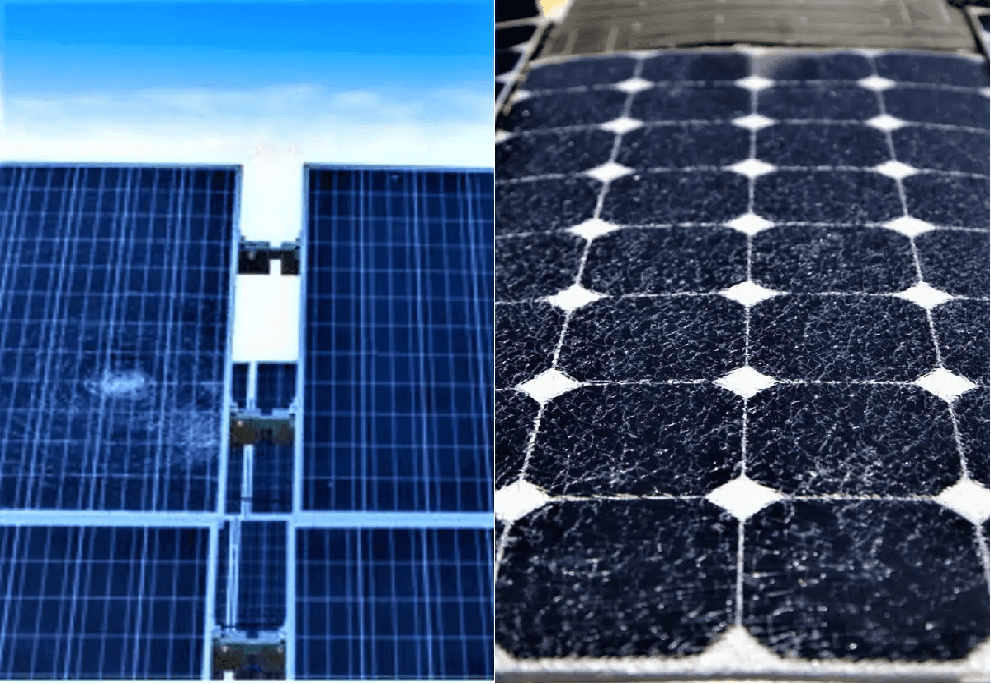
Discolorations
Internal or external factors causing reduced sunlight entry and significant losses.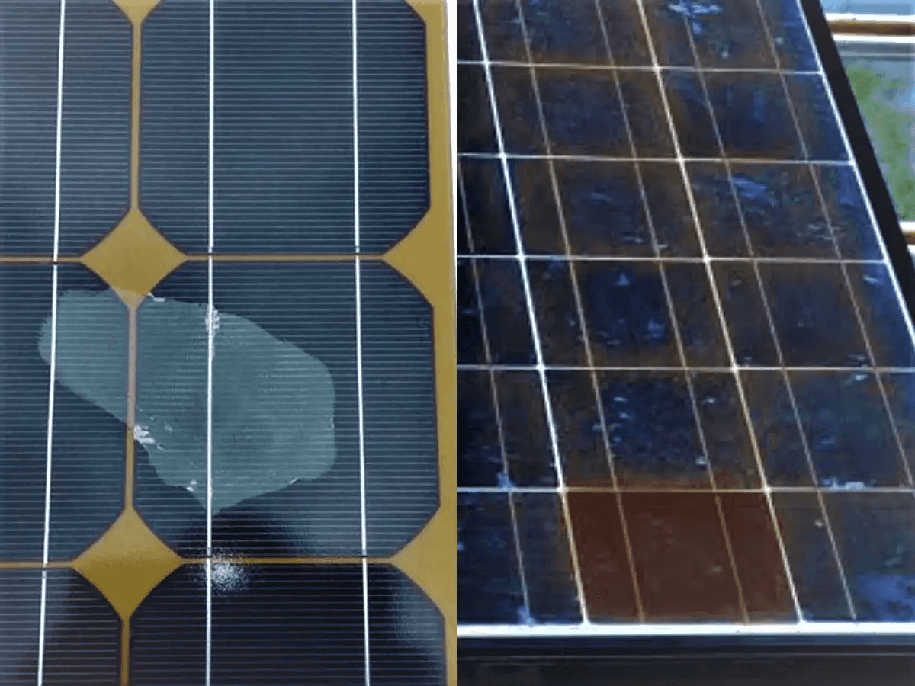
Mounting Failures
Failures in mounting can cause structural issues and lead to decreased panel efficiency.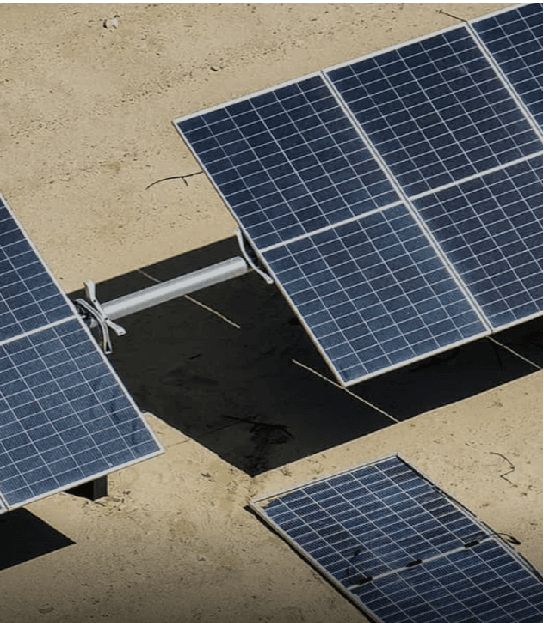
Vegetation
Overgrown vegetation can obstruct panels, reducing overall efficiency.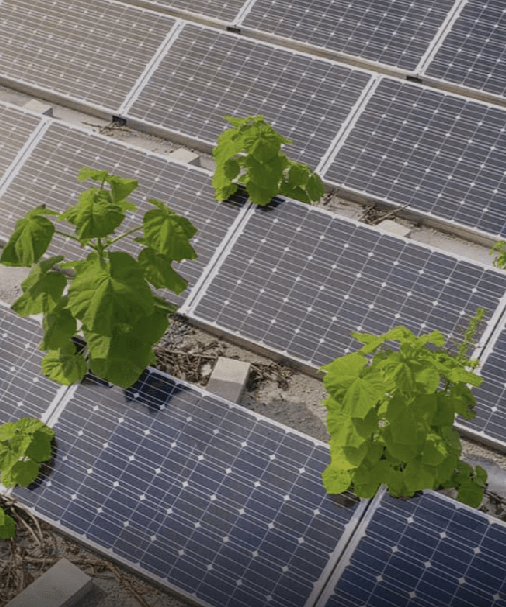
Delamination
Moisture in PV modules leading to delamination, often due to improper lamination methods.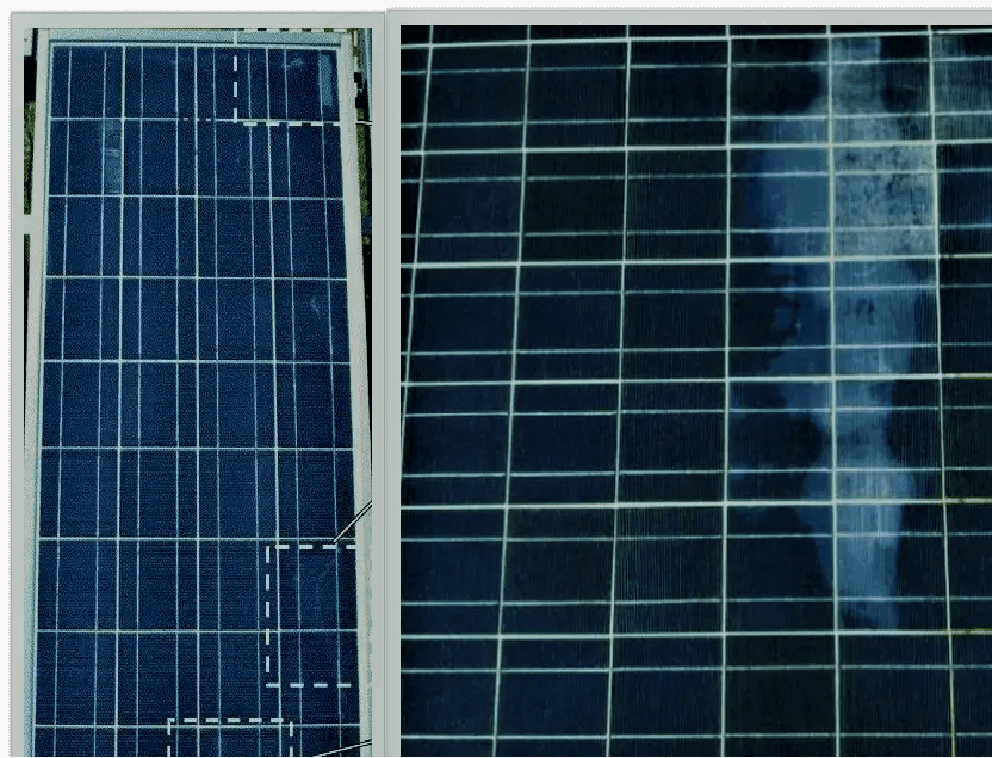
Hotspots
Overloaded regions causing warm spots, leading to increased resistance and short circuits.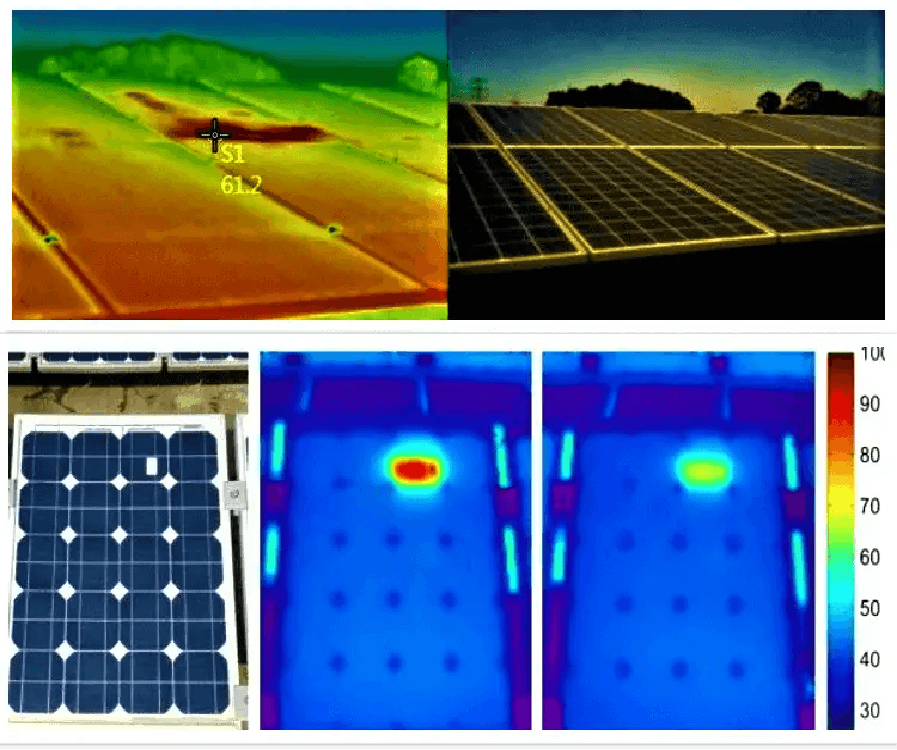
Reverse Polarity
Incorrect wiring can cause reverse polarity, leading to system inefficiencies.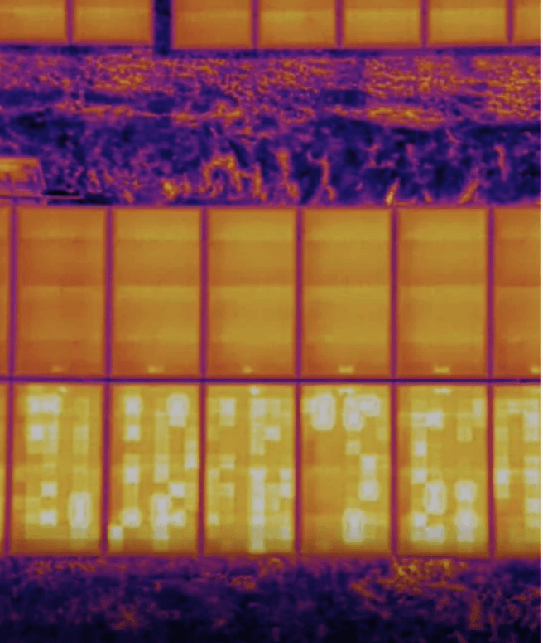
Short-Circuited Module
Short circuits in modules can cause significant safety and efficiency issues.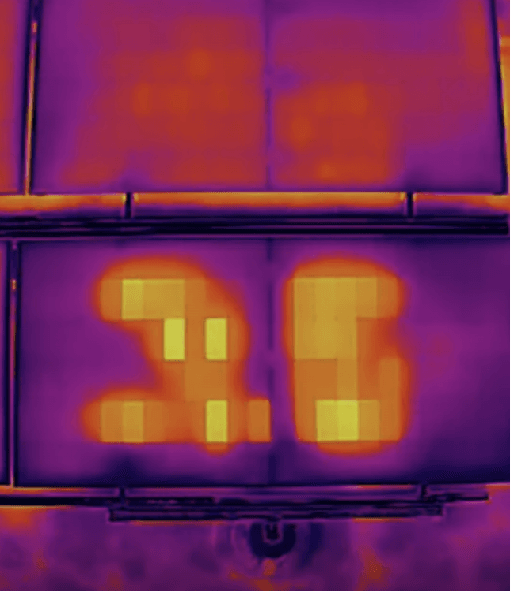
Module Cracking
Cracks in modules can reduce efficiency and lead to further damage.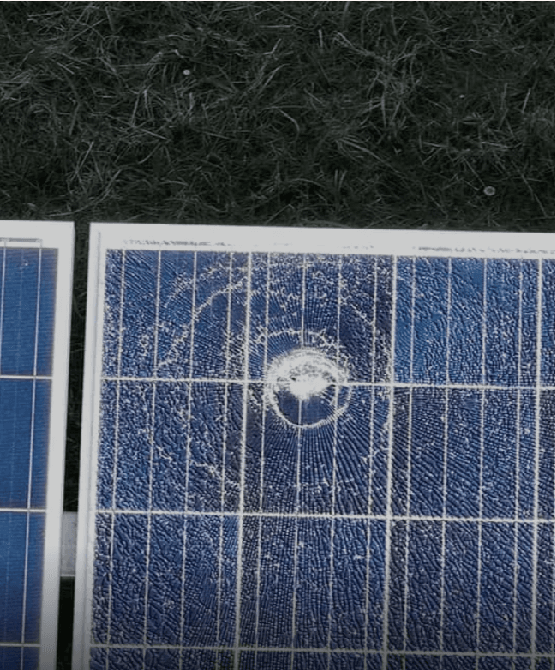
Module Damage
Physical damage to modules often results in decreased energy output.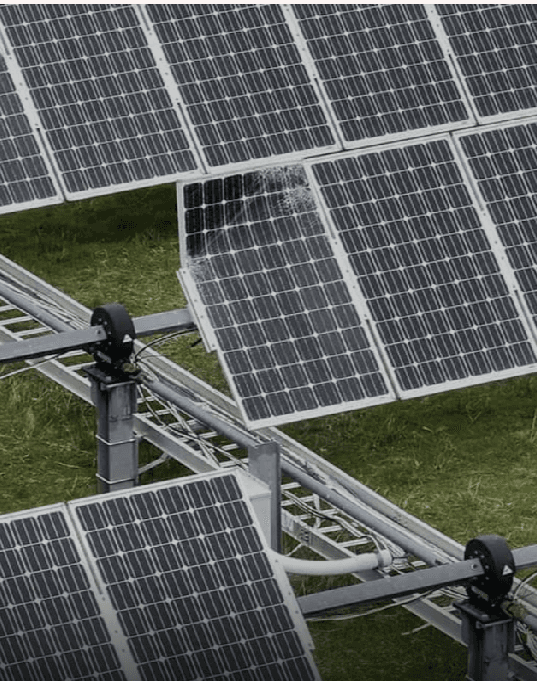
Module Obstruction
Obstructions like dirt and debris can block sunlight, reducing energy production.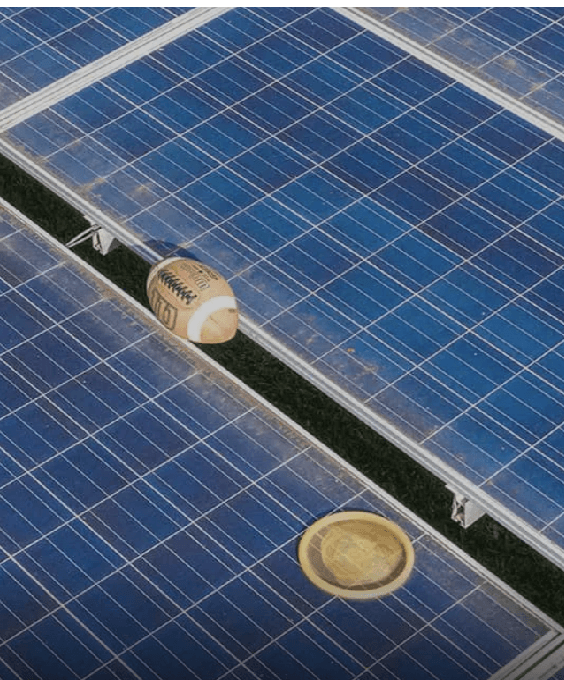
Shading
Shade on panels can drastically reduce efficiency and energy output.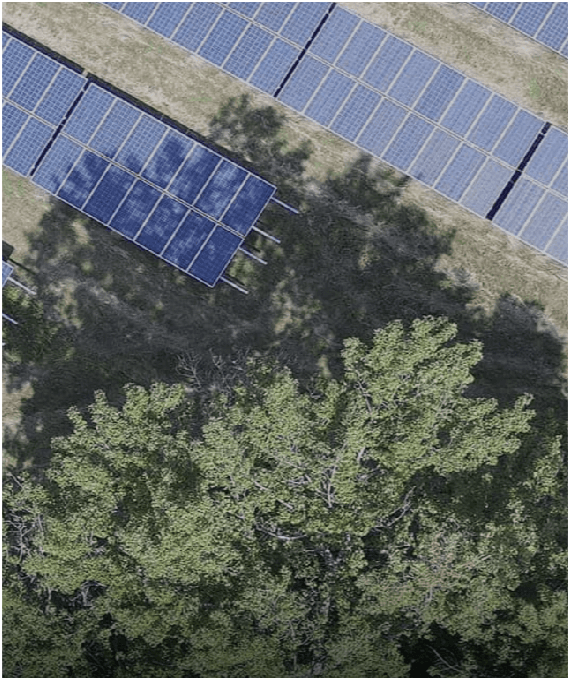
Heated Module
Excessive heat can damage modules and reduce overall system efficiency.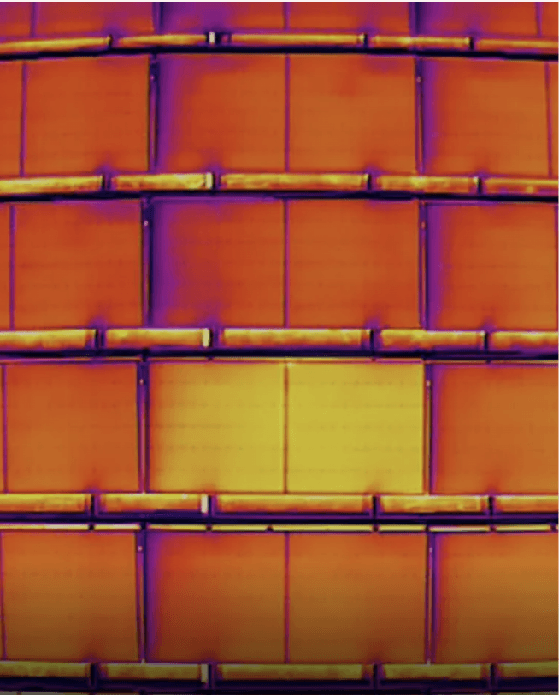
Activated Bypass Diode
Bypass diodes activate to prevent overheating, but frequent use indicates a system issue.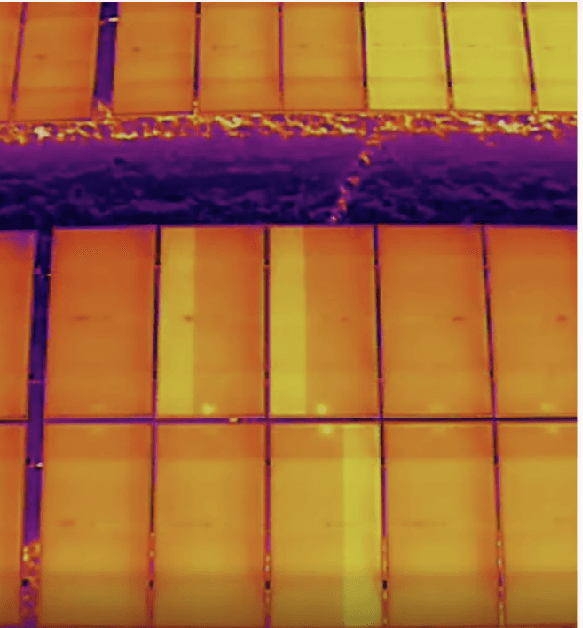
Optimizer Failure
Failures in optimizers can lead to significant energy losses across the system.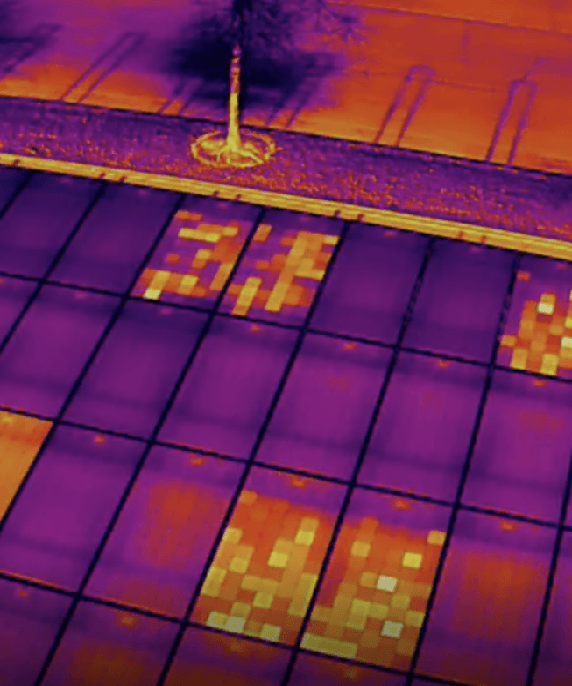
Offline String
An offline string of panels indicates a connectivity issue, reducing system output.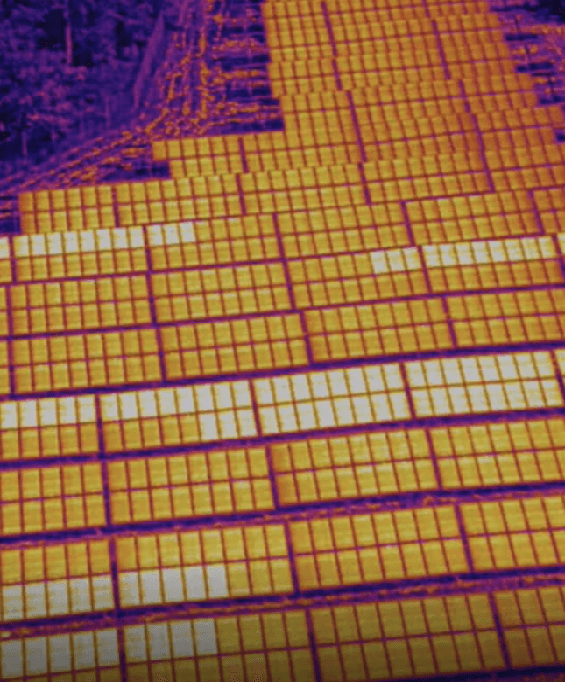
Overheated Junction Box
Excessive heat in junction boxes can cause safety risks and damage to connections.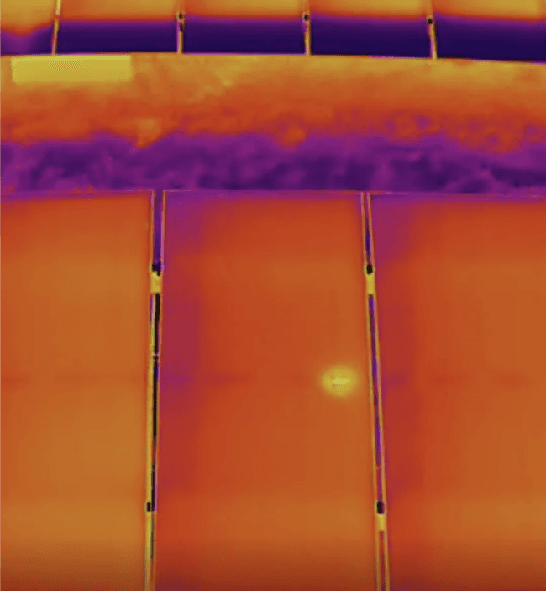
Module Soiling
Accumulation of dirt and debris on modules can significantly reduce efficiency.
Green Energy
Wind turbine inspection & monitoring
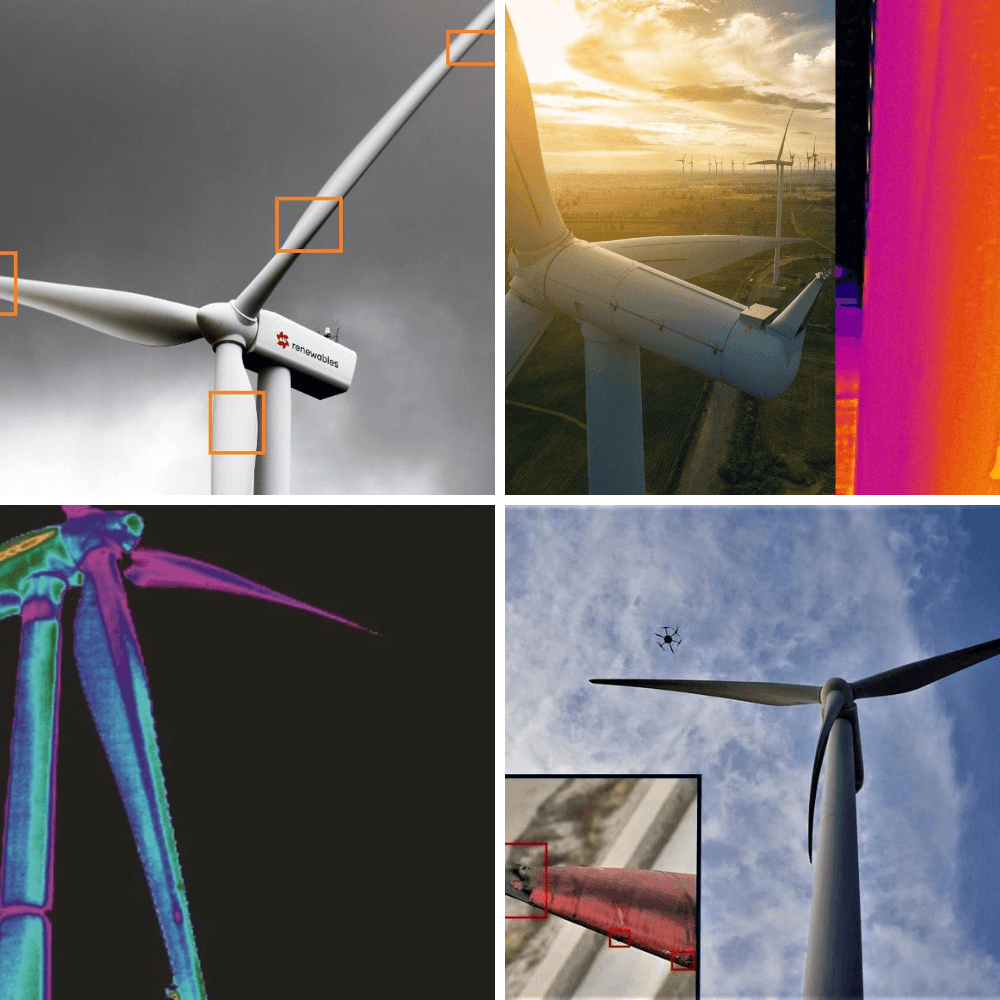
Principle of wind turbine inspection :
- Wind turbine inspections are crucial as they ensure continuous monitoring and maintenance for optimum efficiency. Critical components must be carefully monitored through a systematic maintenance program and regular inspections.
- The turbine blades are a key focus of inspection and maintenance. Damage to the blades reduces efficiency, leading to a loss in power generation and financial losses for the operator.
Methodology we use :
- When inspecting wind turbines, the drone is equipped with a digital camera, a thermographic camera or a combination, depending on the scope of the inspection task. A digital camera provides proof of the visual failures and damages of the tower, nacelle, rotor blades and bolt jointing.
- Thermographic inspection is a non-contact and non-destructive inspection method that makes it possible to examine a large area of the blade for structural defects and weaknesses in the blade.
- With infrared thermography, the drone monitors variations in the surface temperature of e.g. the rotor blades.
Infrared Thermographic Images:
- Non-contact and non-destructive inspection methods
- Visualisation of temperature on large areas of e.g. the rotor blade for comparison
- Examination, measurement and observation of inaccessible or dangerous area
- Detection of hidden defects and failures
- Detection of objects in dark areas
- Detection of erosion and corrosion
- Examination of abnormalities.
The temperature profile of e.g . the blade surface indicates potential defects.
Benefits of wind turbine inspection:
Hail, snow, lightning, rain, salt and dust are just some of the things wind turbine components must endure. Using our drone inspection solution for visual inspection of on and offshore wind turbines provides benefits such as:
- Safe working environment
- Reduced downtime
- High quality images and video
- Access to otherwise inaccessible areas
- Dynamic surveying
- Preventive maintenance planning.
- On Site Blade Rotor Blade Inspection.
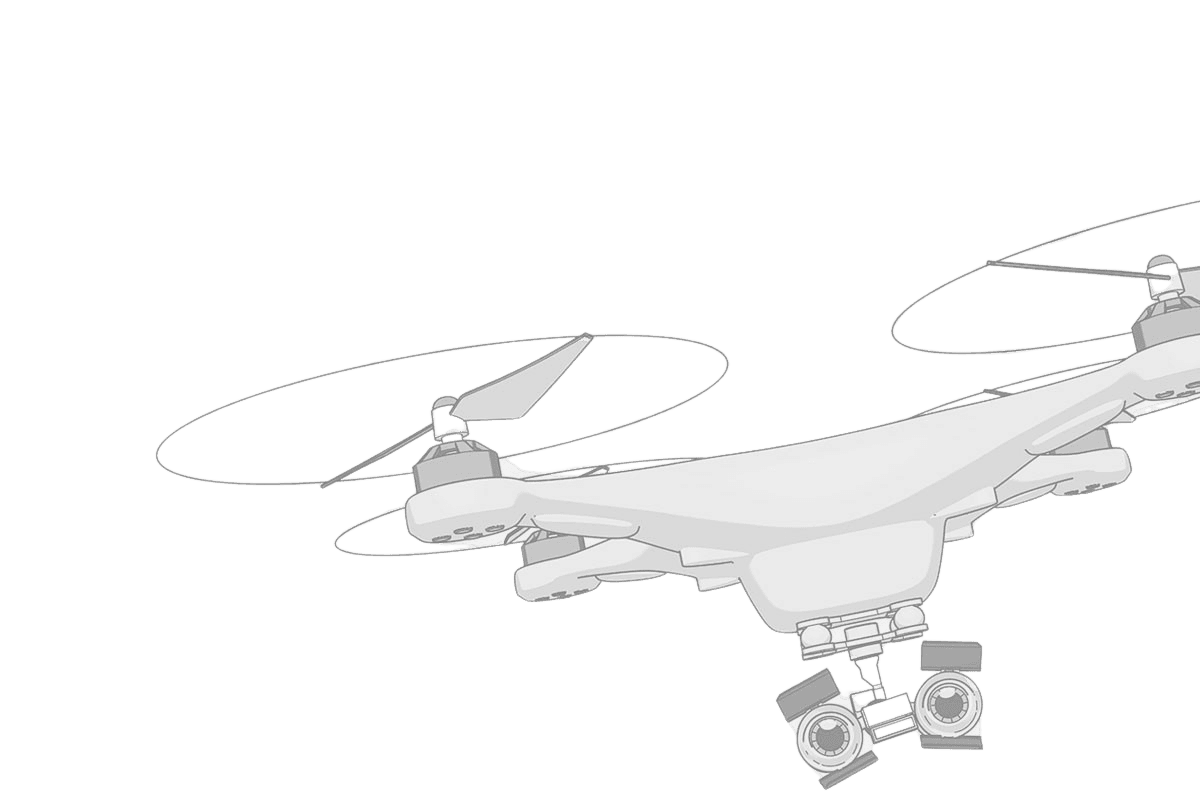
Would you like to collaborate with us?
Get in touch with us now to initiate a collaborative project.